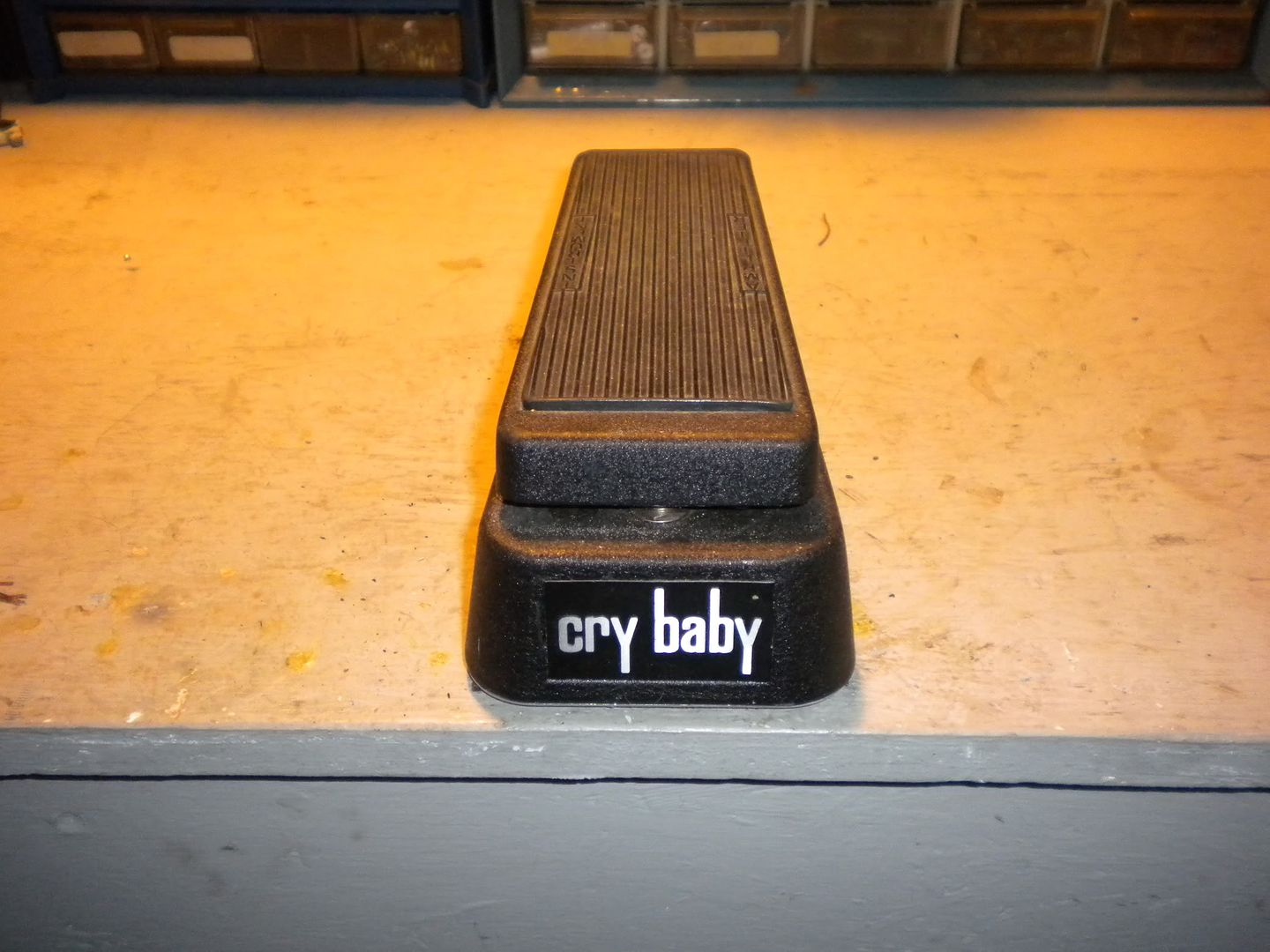
I didn't mind the fact that my original Dunlop Crybaby Wah pedal sounded a little weak, but what I didn't like was it had a switching problem and when I would play in bypass, my guitar didn't sound as great as it did with the wah out of my signal path. With that said and a little inspiration from Mr. Emerson, I decided to modify my wah pedal. There are actually quite a few mods that can be done to this pedal and many websites to research. Here are a list of websites I checked out:
www.wah-wah.co.uk
www.diyguitarist.com/DIYStompboxes/WahMod.htm
I broke the modifications into two main categories to make it really simple. One I wanted true bypass so that my guitar tone didn't sounds bad when the wah pedal isn't engaged and I also wanted Led on/bypass indication as well. Two I wanted to change the way the wah sounded.
The true bypass is done using a DPDT foot switch or a 3PDT foot switch. The advantage of a 3PDT switch is I can have simple led indication. True bypass literary means when the effect is disengaged the signal path is just a wire.

As you can see in the figure above all three switch components are switched at the same time and there are two states. Most effects have one led for when the effect is engaged, but I wanted two leds. Call it overkill, but I like having the indicators this way. 3PDT foot switches can be found on ebay or if you can find a parts supplier.
http://cgi.ebay.com/3PDT-guitar-effects-pedal-footswitch-true-bypass-mod_W0QQitemZ150372119024QQcmdZViewItemQQptZGuitar_Accessories?hash=item2302e071f0
For my wah pedal two components need to be desoldered and a trace needs to be cut.
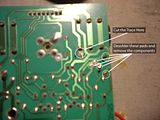
Second, I wanted to mod the sound of the pedal. When the pedal sweeps from the bass to treble, its not that smooth and the mid-range is not at all how I want it. There are a few mods and even one that doesn't require soldering. The mods I did are from this website: http://www.wah-wah.co.uk/. I'm still in the process of tayloring the sound, but the mods I have done are the Vocal Mod with the 68K resistor, Gain & Bass response with a 330ohm resistor, and the Volume mod with a 56K resistor.
I also moved the sweeping pot back a bit to have more of the bass range. This mod can be done just with a phillips screw driver. All you do is unscrew the brace that is against the sweeping bar that has ridges on it to moves the sweeping pot. Then you turn the pot a bit to have either more bass or treble in your foot motion.
Both the websites have some simple and great information on Crybaby Wah mods and should be checked out.
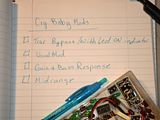
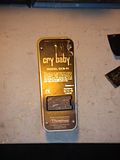
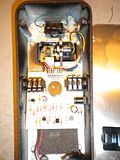
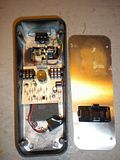
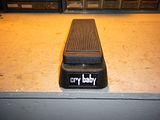
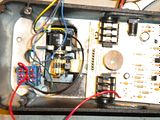
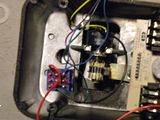
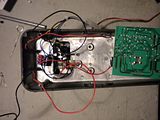
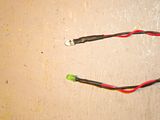
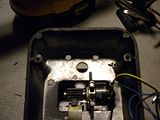
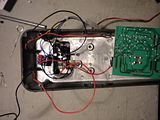

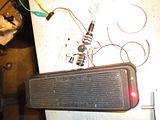
- Ralph Waldo Emerson